
FIRST-M Consulting Ltd.
Failure Investigation
Infrastructure Reliability & Safety
Science & Technology of Materials
From Science to Solutions: Corrosion and Metallurgical Consulting Services
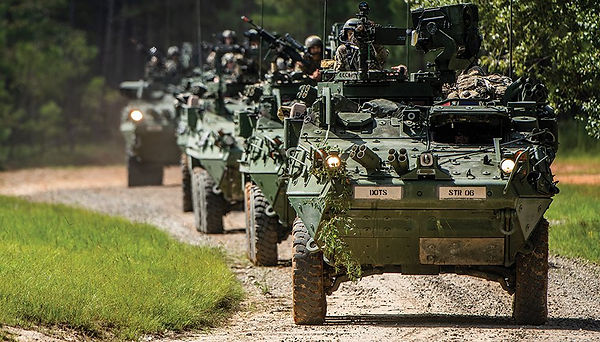
A column of eight-wheeled Stryker combat vehicles moves along a road at Fort Benning, GA, on September 2, 2020, during training. Photo: Patrick A. Albright/U.S. Army.
Dr. Sergei Shipilov was honored with the 2023 Troconis de Rincón Field Applied Technology Award by the Association for Materials Protection and Performance (AMPP) “for achievements in applying engineering and scientific principles to protecting and preserving the U.S. Army’s double V-hull Stryker combat vehicles.” Thanks in part to his research in 2016 and 2017, Canada and the United States were able to send 285 (as of January 2024) light armored combat vehicles to Ukraine to help defend the country against Russia's aggressive actions in the region.
The Field Applied Technology Award is presented annually by AMPP, an international organization representing the largest global community of corrosion and protective coatings professionals, with over 40,000 members in 130+ countries and offices in the U.S., Brazil, Canada, China, Malaysia, Saudi Arabia, and the U.K. This award recognizes individuals, teams, or organizations for “achievements in the application of engineering and scientific principles to the protection and preservation of field structures and property.” To qualify, “a nominee may have used cathodic protection, coatings, inhibitors, materials selection, inter-multi engineering, or other notable efforts to protect and preserve assets.”
Shipilov was presented with the award on March 22, 2023, during the Honoree Night at the AMPP Annual Conference and Expo in Denver, Colorado, which was attended by more than 5,700 attendees from the corrosion and coatings industries worldwide.
Flat-Bottom (FB) Stryker
Stryker is a family of eight-wheel-drive combat vehicles produced for the U.S. Army by General Dynamics Land Systems-Canada (GDLS-C) in London, Ontario. The 20-ton vehicle is based on the Canadian LAV III (LAV stands for light armored vehicle), which first entered service in 1999. Stryker is the primary combat and combat-support platform of the U.S. Army Stryker Brigade Combat Team (SBCT), available in ten variants, including infantry carrier vehicle (ICV), commander’s vehicle (CV), and medical evacuation vehicle (MEV). To simplify logistics and sustainment, all variants share major components, including a six-cylinder, 350-hp Caterpillar diesel engine that delivers a top speed of 62 mph (100 km/h) on the highway and a maximum range of 312 miles (500 km). That high speed is a critical feature of the Stryker, which—armed with an M2 .50 caliber (12.7 mm) heavy machine gun, Mk.19 (or “Mark 19”) 40 mm automatic grenade launcher, or 7.62 mm M240 machine gun—provides protected transport for a nine-man infantry squad and a crew of two. The vehicle was designed to enable an SBCT to maneuver more easily in close and urban terrain and to provide protection in open terrain. As a deployable fighting vehicle, Stryker offers a balance between tanks and armored personnel carriers: it is more lethal than light vehicles like Humvees yet is more lightweight and maneuverable than heavyweight M1 Abrams main battle tanks. Strykers operate well in snow, mud, and sand. They can be deployed by C-5 Galaxy (carries 4 vehicles), C-17 Globemaster III (3 vehicles), and C-130 Hercules (1 vehicle) aircraft and be combat-capable upon arrival in any contingency area. These attributes made the Stryker “the Army’s first true system-of-systems,” enabling the SBCT’s unique, organic combined arms capability.
The Double V-hull (DVH)

A Stryker vehicle (General Lee) lies on its side after surviving a buried IED blast while conducting operations in Iraq in April 2007 (Photo: C-52 of 3/2 SBCT). Like all light armored combat vehicles then, General Lee was Stryker’s basic flat-bottom (FB) variant. Too many losses in Iraq and Afghanistan—e.g., only in the few months of 2009, the 5th Stryker Brigade lost 21 soldiers, 40 more wounded, to IEDs and landmines—prompted the U.S. Army to examine modifications to Stryker to make it more resistant to land mines. Efforts resulted in creating a DVH design with, as thought, significantly increased survivability and protection. The DVH vehicles, however, experienced structural cracking like that shown in the figure below (S.A. Shipilov, DoD CorrDigest, 1(2), 2018, 18-24).
The newer DVH configuration was created in response to high casualties from roadside bombs and improvised explosive devices (IEDs) in Afghanistan and Iraq from 2003 to 2010, where flat bottom (FB) Strykers were in use. (Note: Since 2001, during the war in Afghanistan, there have been over 70,000 incidents involving IEDs, which were responsible for 90% of all U.S. casualties.) The lower hull, initially FB, was redesigned to DVH to deflect blasts better away from the vehicle; it was supposed to provide soldiers inside with enhanced protection and survivability from IEDs and roadside bombs. In May 2011, Mike Cannon, GDLS’ Senior Vice President of Ground Combat Systems, said, “We wanted to take advantage of the V shape and get the center of the vehicle farther away from the ground to aid survivability” (Kris Osborn/U.S. Army). “Soldier survivability is the Army’s number-one priority. Once we determined that the DVH effort was an achievable and acceptable risk, we swiftly engaged in executing the robust program,” added Col. Robert Schumitz, Project Manager for SBCT. The first 150 new Strykers arrived in Afghanistan in the summer of 2011.
Cracks on the Lower-Right Fender
Despite all the best intentions, after being put into use, DVH Strykers across at least three variants (ICVV, CVV, and MEVV) experienced structural cracking on the lower-right fender behind the second steering wheel, directly under the vehicle commander’s seat (see figure on the right). The problem brought into question the ability of DVH to withstand explosives and roadside mines. The cracks put soldiers’ lives at risk, affected DVH vehicles’ availability in Afghanistan, and posed a threat to large-scale ground combat operations (LSCO) using DVH Strykers. All this required immediate attention. In such a critical situation, the U.S. Department of Defense (DoD), despite all its resources, an annual budget of nearly $800 billion, and dozens of research institutions and academies, could not find for years a subject-matter expert capable of explaining the cause of the cracks and finding a solution to the life-threatening problem. Then, lucky for the U.S. and Allied armies, Shipilov agreed to help in early 2016.
Who, if not Shipilov?
It happened not for the first time that DoD—when dealing with materials degradation and corrosion problems—should rely on the experience and expertise of Shipilov, a Canadian of Russian descent, born and educated in the former Soviet Union at the pick of the Cold War and commissioned as a Lieutenant-Engineer Officer in the Soviet Army Reserve after completing ROTC with distinction in 1981—such a historical irony.
He is the only expert from the U.S. Department of Energy’s (DoE) National Laboratories, “a preeminent federal research system, providing the nation with strategic scientific and technological capabilities,” who was ever invited to the U.S. Department of Defense (January 14, 2016) to help to institute corrosion prevention and control strategies under DoD directives in engineering design and materials selection for new acquisitions [1]. Two strategic initiatives [2,3] he has developed at the request of the Corrosion Policy and Oversight Office within the Office of the Under Secretary of Defense for Acquisition, Technology, and Logistics were called by DoD “the only way to visibly decrease the cost of corrosion” [4], which exceeds $20 billion per year in the U.S. Armed Forces. On October 9, 2015, U.S. Navy Vice Admiral Kendall L. Card (Ret.), the former Commanding Officer of the Nimitz-class nuclear-powered aircraft carrier USS Abraham Lincoln (CVN 72), Deputy Chief of Naval Operations and Director of Naval Intelligence, requested a meeting with Shipilov to learn if and how DoE’s National Lab researchers could help DoD dealing with corrosion [5]; surprisingly, the possibility, which could substantially change the situation with corrosion in the U.S. military, and potentially save billions of dollars, was never discussed either at DoD or DoE. After the meeting, Shipilov initiated research on irradiation-assisted fatigue corrosion cracking (IAFCC) in naval reactor internals, causing substantial delays in the maintenance of nuclear-powered aircraft carriers and submarines in service with the U.S. and Allied navies [6]. In 2020, he assessed—for the first time it was done—the impact of materials degradation and corrosion on the U.S. Navy aircraft readiness for the National Commission on Military Aviation Safety created by Congress [7].
In 2016, his involvement appeared to be the only chance for DoD to improve its infantrymen’s protection and safely perform large-scale ground combat operations (LSCO) using DVH Stryker vehicles.
Before his involvement [8], GDLS-US and Oak Ridge National Laboratory (ORNL), after many months of work, entirely failed the investigations. The ORNL team, including five highly qualified researchers with 125 years of combined experience after earning doctorates from the best U.S. universities, even contrived to destroy substantial evidence because they did not know what to do and tried to do at least something not necessarily correct or needed. It is worth noting that GDLS is “a global leader in designing, engineering, producing, supporting and sustaining tracked and wheeled

(1) In the presence of such a through-wall crack more than 40 cm long and 1 mm to 2 mm wide—like was in the DVH Stryker ICVV‐0285 (bottom photo)—even the toxic smoke produced by detonating explosives, if it penetrates through the crack, could be dangerous and fatal for soldiers in the vehicle, especially when they cannot leave it in the case of a battle. (2) Because the cracking occurred where the 2-speed transfer case (T-case), weighing several hundred pounds, was mounted to the 7.5-mm-thick fender, the problem could cause partial or total transmission failure, making the vehicle challenging or impossible to drive. If it happens under fire in the middle of a battle, the soldier’s safety is at risk, and depending on the damage state, all could be captured or killed if time allows. (3) Even on the road far from the frontline, the inoperable T-case would nullify all benefits of the 350-hp Caterpillar diesel engine. (4) In the worst-case scenario, an IED blast or a direct hit by a rocket-propelled grenade (RPG) into the cracked fender—e.g., when the second steering wheel turned left, totally opening it—could fracture the fender and seriously wound or kill the commander and those sitting nearby. (5) If a 20-ton vehicle’s fender
cracks, it must be removed from service and taken to a repair depot, which is not a suitable option for the armed forces involved in military operations. Even if the crack is tiny and not visible to the naked eye, no combat vehicle with a cracked lower fender can be used on the battlefield. The safety and lives of U.S. soldiers were at risk. This was the seriousness of the problem when Shipilov was called in to help.
military equipment,” and ORNL positions itself as “the U.S. Department of Energy’s largest science and energy laboratory with over 4,600 staff” and “home to the nation’s most comprehensive materials research program;” the latter was the main reason why the U.S. Army approached ORNL for help. The two vast organizations, each managing a multi-billion-dollar science and technology portfolio, used all capacities of the GDLS Materials Engineering and Survivability/Armor Design Laboratory (consisting of “55 engineers with widely disparate backgrounds ranging from materials science to armor engineering”) and ORNL Materials Science and Technology Division (in which 200+ researchers had Ph.D. in materials science and engineering and $140 million was allocated for research) and the nation’s very best equipment for materials studying, which cost tens of millions of dollars (though was not needed for this investigation at all). All their incredibly unique equipment and multi-month efforts, costly for the military and taxpayers, were useless, as in many other cases. (For example, just a year earlier, ORNL completely failed another, much simpler project for the U.S. Marine Corps, for the useless outcomes of which the Department of the Navy paid upfront $4.2 million of public money, according to Matt Koch, then U.S. Navy Corrosion Control and Prevention Executive [9].)
Shipilov’s experience and expertise—on which DoD could only hope, if not pray hard—allowed him to determine (for the first time it was done) the cause and mechanism of cracking. He did it in minutes when he stopped on January 5, 2016, to look at the fender’s cracked piece on his way to the parking late in the evening after hours, using only his cell phone camera to collect critical evidence [8].
After being officially asked by the U.S. Army to help, he was the first to reveal that cracking on the lower-right fender was the generic problem of DVH [10] rather than of a dozen vehicles with already broken fenders, as initially thought by the military. The conclusion meant that the entire DVH fleet was sensitive to this type of cracking. He also found that lower fenders were occasionally made the steel that did not meet the military specification MIL-DTL-46100E for high hardness armor (HHA) steel [11]. The steel had the incorrect microstructure, and its hardness was 30% below the specified minimum of HRC 50. This meant that fenders made of this steel must not be used in the production of armored vehicles. Even if the fenders did not have any cracks, they could not shield soldiers from blasts effectively. When the fenders had cracks, any military mission became dangerous for the soldiers and the crew. Although it was thought (by the Army leadership) that DVH could double soldiers’ survivability against IED and blast threats compared to the basic FB hull, he estimated that stress enough to break the cracked fender made of HHA steel with UTS of 1750 MPa could be as low as 400 MPa and even 30 MPa depending on the crack length, i.e., almost 60 times less than expected; no way such a fender would withstand a blast. Finally, he found and proposed—for the first time in five years—the only possible (and inexpensive for the military) solution to the entire problem during his visit to the Retrofit and Stryker National Repair Center at Joint Base Lewis-McChord (JBLM), the DoD’s premier military installation on the West Coast, in February 2017 [12].
The Complexity of the Problem
Was it so difficult to conduct and complete the investigation? Were conclusions made by Shipilov obvious? Was the only possible and reliable solution for the problem (technically simple and inexpensive for DoD) apparent? Why did the problem have neither a proper explanation nor a
solution for years before his involvement? “Anyone can find the switch after the lights are on” (Confucius).
To solve this (engineering) problem [8,10-14], it was necessary not only to have advanced knowledge in and a deep understanding of metallurgy, engineering mechanics, fracture mechanics, stress-strain analysis, metal physics, fatigue, fractography, and engineering design—in each of which GDLS and National Laboratories undoubtedly have the most knowledgeable and qualified scientists and engineers in the nation—but more importantly, it was necessary to have a wealth of experience in and understanding of how to use the fundamental principles of these and some other disciplines at their intersection [13, 15]. The ability to see the whole Stryker as one piece (not the crack alone), including its design and functionality of various components, especially in the move, was also an essential requirement.
What If …
“What if” games are never easy, but it ought to be interesting to imagine how the U.S. and Allied ground forces, including the Canadian Army, would have behaved if the cracking problem had become massive and still unsolved. Would they accept using the vehicles built on the generically defective DVH platform in their ground combat operations, knowing it’s unsafe for soldiers who put their lives on the line defending the nation? How would they deal with the situation if Greg Updike, Project Manager for Stryker Brigade Combat Team (SBCT), did not hire Shipilov on behalf of the U.S. Army after talking with him for the first time in January 2016 when GDLS had already failed their investigation (in April 2015) [16] and the ORNL team—after being on the wrong track all the time—finally acknowledged that was no closer to any conclusion after months of the investigation and dropped from the project on January 6, 2016?
At about the same time, in 2016-2017, Shipilov was the principal investigator for the world’s most challenging and demanding R&D project and the only groundbreaking project ever conducted within the DoE’s National Laboratory System in metallurgy/materials science and corrosion [17-19]. The project was focused on one of the highest priority materials degradation problems, affecting the longevity of the commercial water-cooled nuclear power reactors worldwide and, being associated with the integrity of aging naval reactors, adversely affecting the ability of the U.S. and Allied navies to respond rapidly to national security and foreign commitments [6]. No nuclear research center/team around the globe was ready to carry out such a project; no one was even aware that today’s knowledge, science, and technology allow it. Among other projects in those months, at the request of the U.S. Senate Appropriations Subcommittee on Energy and Water Development, he created and led a multidisciplinary team of researchers conducting “the most comprehensive study in the field of the external [soil-side] corrosion of water mains to date” (DIPRA, 2016) [21-23]; this was the first extensive study based on advanced scientific methods to determine the causes and most effective measures to reduce corrosion’s impact—with an annual cost of over $70 billion—on the U.S. water and wastewater systems.
How did Shipilov become available to DoD at the right time? It did not happen as one would expect. Contrary to common sense expected from those who have never worked at ORNL, the senior management of ORNL prohibited him in writing (!), under the threat of dismissal, from working on the project aimed to protect soldiers against blasts and IEDs during combat operations in Afghanistan, though it was ORNL that officially signed the $130,000 contract with the U.S. Army specifically for Shipilov’s one-man work on this project.
Aftermaths
-
In August 2017, Shipilov’s investigation, which he completed for the U.S. Army in June 2016, earned him the Best Paper Award at the 2017 DoD-Allied Nations Technical Corrosion Conference, sponsored by the Office of the Secretary of Defense. His award-winning paper [14] “journaled the study of fielded double V-hull Stryker light armored vehicles that were found to have structural cracking issues that affected availability,” as the DoD’s citation read.
-
In June 2018, his success allowed or at least played a role in placing a $258 million (USD) contract with GDLS to upgrade 116 Stryker FB vehicles to the improved DVHA1 configuration with an estimated completion date of March 2020.
-
In January 2019, the DoD placed another contract with GDLS to upgrade up to 2,525 Stryker FB vehicles to the improved DVH configuration, now designated as the “DVHA1 engineering change proposal (ECP) version of the Stryker vehicle.”
-
In August 2019, Canada’s government placed a $3 billion (CAD) contract with GDLS to supply the Canadian Army with 360 light armored vehicles (LAV 6.0) built on the same DVH platform as U.S. Army Stryker—now designated as DVHA1—of which blast protection was improved based on Shipilov’s research.
-
In June 2020, the DoD awarded GDLS a $2.48 billion contract to produce more upgraded “Stryker DVHA1 engineering change proposal (ECP) vehicles;” the number of vehicles was not disclosed, but the work should take just under seven years.
-
In July 2022, Canada’s government sent the first 39 of the 360 DVHA1 LAV 6.0 vehicles, ordered in August 2019, to war-torn Ukraine.
-
In November 2022, Canada’s government signed a new $165 million contract with GDLS for an additional 39 LAVs to replace donated vehicles to Ukraine.
-
Since January 2023, the Biden administration has sent 246 Strykers to Ukraine as part of its military aid.
S.A. Shipilov, Corrosion and materials research to meet 21st-century defense needs
“Defense Institute for Science and Technology of Corrosion (DISC) at ORNL and Master’s Degree in Materials Science and Engineering with Concentration in Corrosion Engineering at UTK,” presented at Meeting of the U.S. Department of Defense Office of Corrosion Policy and Oversight (CPO) and Military Corrosion Control and Prevention Executives, February 17, 2016. Shipilov SA (2016, February 17) Corrosion and materials research to meet 21st-century defense needs. Presented in a teleconference meeting of the DoD Office of Corrosion Policy and Oversight (CPO) and Military Department Corrosion Control and Prevention Executives, chaired by CPO Director DJ Dunmire.
References:
-
S.A. Shipilov, “Advances and Challenges in Understanding the Influence of Environments on the Long-term Stability and Integrity of Materials: A Means of Avoiding Failures in Aircraft Structures,” Meeting at the DoD Corrosion Policy and Oversight (CPO) Office within the Office of the Under Secretary of Defense for Acquisition, Technology, and Logistics (OUSD [AT&L]), U.S. Department of Defense, Alexandria, VA, January 14, 2016.
-
S.A. Shipilov, “DoD-focused Master’s Degree Program in Corrosion Engineering,” Leadership Meeting, College of Engineering, University of Tennessee, Knoxville, TN, February 3, 2016.
-
S.A. Shipilov, “Corrosion and Materials Research to Meet 21st-Century Defense Needs: Defense Institute for Science and Technology of Corrosion (DISC) at ORNL and Master’s Degree Program in Materials Science and Engineering with Concentration in Corrosion Engineering at UTK,” Teleconference Seminar, DoD Office of Corrosion Policy and Oversight (CPO) Leadership and Military Department Corrosion Control and Prevention Executives, February 17, 2016.
-
D.J. Dunmire (U.S. Department of Defense Office of Corrosion Policy and Oversight), Personal Communication, 2017 DoD-Allied Nations Technical Corrosion Conference, Birmingham, AL, August 9, 2017.
-
S.A. Shipilov, “Corrosion and Reliability of Advanced High-Performance Alloys in the Military Services,” Meeting with U.S. Navy Vice Admiral Kendall L. Card (Ret.), U.S. Department of Defense and Intelligence Community Integration, Global Security Directorate, Oak Ridge National Laboratory, Oak Ridge, TN, October 9, 2015.
-
S.A. Shipilov, “An Experimental Irradiation Assembly for the Investigation of Corrosion Fatigue Crack Growth in the Structural Components of Naval Reactors, ” Proc. 2019 DoD-Allied Nations Technical Corrosion Conference, Paper No. 2019-0099 (Washington, DC: Department of Defense, 2019).
-
S.A. Shipilov, "Impact of Corrosion on the United States Navy’s Overall Readiness,“ Report to the National Commission on Military Aviation Safety/Congressional Committee (Toronto, Ontario: FIRST-M Consulting Ltd., February 14, 2020).
-
S.A. Shipilov, “Analysis of Cracked Stryker Hull Specimen,” Corrosion Science and Technology Group Seminar for Greg Updike, Project Manager for Stryker Brigade Combat Team (SBCT), Oak Ridge National Laboratory, Oak Ridge, TN, January 6, 2016.
-
M. Koch, Discussion, DoD Office of Corrosion Policy and Oversight (CPO) Leadership and Military Department Corrosion Control and Prevention Executives, 2015 DoD-Allied Nations Technical Corrosion Conference, Pittsburgh, PA, November 18, 2015.
-
S.A. Shipilov, “Analysis of Cracked Stryker Hull Specimen and Review of the Technical Report ‘Transfer Case Weld Cracking (April 14, 2015)’,” Corrosion Science and Technology Group Seminar for Greg Updike, Project Manager for SBCT, and Colonel Stephen Thomas, Product Manager/SBCT Production and Variant Management, U.S. Army’s Combat Ground Vehicle Development Project Office, Oak Ridge National Laboratory, Oak Ridge, TN, June 23, 2016.
-
S.A. Shipilov, B. Pint, Analysis of Cracked Stryker Hull Specimen, Report (Task 2) U.S. Army Stryker Brigade Combat Team (SBCT), Oak Ridge National Laboratory, U.S. Department of Energy Contract DE-AC05-00OR22725, June 24, 2016.
-
S.A. Shipilov, “A New Design for Mounting a Transfer Case (T-Case) on DVH Stryker Vehicles,” Update for Greg Updike, Project Manager for SBCT, Retrofit and Stryker National Repair Center, Joint Base Lewis-McChord (JBLM), Tacoma, WA, February 6, 2017.
-
S.A. Shipilov, “Cracking Resistance of High Hardness Armor (HHA) Steel and Mounting a Transfer Case (T-Case) on DVH Stryker Vehicles,” Teleconference Seminar/Joint Meeting of ORNL Corrosion Science and Technology Group and GDLS Materials Engineering and Survivability and Armor Design Laboratory, January 11, 2017.
-
S.A. Shipilov, Corrosion Fatigue Crack Propagation in a Stryker Combat Vehicle,” Proc. 2017 DoD-Allied Nations Technical Corrosion Conference, Paper No. 2017-761104, S.A. Shipilov, “Cracking Resistance of High Hardness Armor (HHA) Steel and Mounting a Transfer Case (T-Case) on DVH Stryker Vehicles,” Teleconference
Seminar/Joint Meeting of ORNL Corrosion Science and Technology Group and GDLS Materials Engineering and Survivability and Armor Design Laboratory,
January 11, 2017. Reprinted as a Cover Story in DoD CorrDigest 1:2 (2018), 18-24, and featured on the homepage of the U.S. Department of Defense Corrosion Policy and Oversight Office’s website, 2018-2019. -
S.A. Shipilov, “Mechanism of Crack Initiation and Propagation in a Stryker Light Armored Vehicle,” Materials Science and Technology 2018 Conference (MS&T 2018), Columbus, OH, October 14-18, 2018.
-
S.A. Shipilov, B. Pint, “Review of the Technical Report Transfer Case Weld Cracking (April 14, 2015),” Report (Task 1) U.S. Army Stryker Brigade Combat Team (SBCT), Oak Ridge National Laboratory, U.S. Department of Energy Contract DE-AC05-00OR22725, June 3, 2016.
-
S.A. Shipilov, In Situ Electrochemically Controlled Irradiation-Assisted Corrosion Fatigue Crack Growth in Austenitic Stainless Steels, LDRD Project: Transformational Nuclear Science and Technology, LOIS ID 8384, Semiannual Progress Report (October 2016-March 2017), Oak Ridge National Laboratory, Oak Ridge, TN, March 22, 2017.
-
S.A. Shipilov, In Situ Electrochemically Controlled Irradiation-Assisted Corrosion Fatigue Crack Growth in Austenitic Stainless Steels, LDRD Project: Transformational Nuclear Science and Technology, LOIS ID 8384, Annual Progress Report (October 2016-July 2017), Oak Ridge National Laboratory, Oak Ridge, TN, August 14, 2017.
-
S.A. Shipilov, “An Experimental Irradiation Assembly for the Performance of In-Reactor IASCC Tests Under Cyclic Loading,” Materials Science and Technology 2018 Conference (MS&T 2018), Columbus, OH, October 14-18, 2018.
-
S.A. Shipilov, “Evaluation of Zinc-Coated Ductile Iron Pipe,” Seminar/Joint Meeting of ORNL Corrosion Science and Technology Group and Ductile Iron Pipe Research Association (DIPRA), Oak Ridge National Laboratory, Oak Ridge, TN, August 30, 2016.
-
S.A. Shipilov, K. Unocic, B. Pint, Evaluation of Zinc-Coated Ductile Iron Pipe, Progress Report ORNL/TM-2016/628, Oak Ridge National Laboratory, U.S. Department of Energy Contract DE-AC05-00OR22725, October 7, 2016.
-
S.A. Shipilov, “Drinking Water Infrastructure Protection and Lifetime Prediction: Water Supply Distribution Systems,” Joint Meeting of ORNL and Lawrence Berkeley National Laboratory’s (LBNL) Water-Energy Resilience Institute, Oak Ridge National Laboratory, Oak Ridge, TN, July 6, 2017.
-
S.A. Shipilov, “Water Infrastructure Corrosion: What Prevents Us from Preventing It?” Materials Science and Technology 2018 Conference (MS&T 2018), Columbus, OH, October 14-18, 2018.