
FIRST-M Consulting Ltd.
Failure Investigation
Infrastructure Reliability & Safety
Science & Technology of Materials
From Science to Solutions: Corrosion and Metallurgical Consulting Services
FIRST-M LEADERSHIP
Sergei Shipilov, Ph.D., FAMPP, FASM, FCIM
President
EDUCATION
-
Ph.D., Materials and Corrosion, Institute of Physical Chemistry, USSR Academy of Sciences, Moscow, 1987
-
Research Internship, Chemistry/Materials Science, Institute of Physical Chemistry, USSR Academy of Sciences, 1981–1983
-
Lieutenant Engineer Officer (Reserve), Army ROTC, Moscow Institute of Petroleum and Gas Technology, 1981
-
Mechanical Engineer’s Degree (5-year program), Moscow Institute of Petroleum and Gas Technology, 1981
-
Secondary Education: Arkhangelsk High School No. 5, Arkhangelsk, Russia, 1976 [read more]

Academic appointment: Adjunct Professor, University of Science and Technology Beijing, 2018–present
Dr. Shipilov is an internationally recognized expert in microstructure/properties relationships, long-term performance, and integrity of materials under in-service conditions. His research investigates how materials respond to mechanical stresses, corrosive environments (both natural and technological ), and high levels of ionizing radiation and how in-service conditions affect materials’ behavior, particularly their resistance to corrosion, fatigue, and environmentally assisted cracking. His expertise covers a broad range of applications, from space technology and nuclear power to naval aviation, submarines, and oil and gas production—where the degradation of materials (their properties) over time can lead to severe accidents, environmental contamination, human casualties, and financial losses, often exceeding hundreds of millions of dollars (1). As a researcher, he is renowned for his ability to create innovative scientific developments and convert them into practical engineering outcomes (Prof. E.M. Gutman, 2012). Among his numerous national and international awards, a major highlight is being selected as the 2025 recipient of the Morris Cohen Award from The Minerals, Metals & Materials Society (TMS). This award is one of the most prestigious honors in materials science and engineering, presented annually to a materials scientist who has made “outstanding contributions to the science and/or technology of materials properties.” He is the first materials scientist from Canada and the first corrosion expert to be included in the select group of twelve distinguished materials scientists from the U.S. and Europe who have received this accolade since 2012. He was recognized “for advances in the fundamental understanding of environmental effects on the mechanical properties and integrity of materials.”
Shipilov has researched a wide range of structural materials, from conventional to advanced and specially designed, including high-strength low-alloy (HSLA) steels, stainless steels, carbon steels, cast irons, and titanium, aluminum, magnesium, and nickel-based alloys. His research findings have been implemented in aerospace, nuclear, military, and naval technology, pipelines, medical implants, and public infrastructure, saving at least U.S.$1 billion (or its equivalent in a foreign currency) by preventing severe (and highly expected) accidents in nuclear and petroleum technologies. Additionally, his research has led to securing multi-billion-dollar contracts for the production of space and military equipment. This includes orbital modules for the International Space Station (ISS), upgraded Progress M cargo spacecraft, hulls for nuclear-powered submarines, and more than 3,000 double V-hull (DVH) Stryker/LAV 6.0 light armored vehicles (each costing over U.S.$6 million) for the U.S. and Canadian Armies. Since the mid-1980s, he has provided consulting services to major international industries and governments, successfully resolving both (simple) issues related to corrosion in domestic settings and complex problems associated with nuclear and deep-ocean challenges. Many of these complex problems were deemed unsolvable until he was called in for assistance....
TESTIMONIALS
His worldwide status in these areas is supported by the fact that his expertise has been sought by companies, government agencies, research groups, and leading research institutions in 17 countries on five continents. He has been invited to deliver lectures and seminars at 26 universities and 17 research centers across 11 countries and conducted workshops for industry specialists in Canada, India, and Iran. He was interviewed three times for international technical journals on corrosion-related issues (in 2013 and twice in 2015), and one of the interviews was selected as the journal’s feature article and cover story. In 2016, he was invited to the Department of Defense (DoD) to help develop science-based strategies for preventing and mitigating corrosion in the U.S. Armed Forces; his proposals were referred to by the DoD Corrosion Policy and Oversight referred to his proposals as “the only way to reduce the [corrosion] costs” (D.J. Dunmire, 2017), which exceed $20 billion a year. (Note: An additional task was to clarify a mix-up created by the Defence Science Board Task Force on Corrosion Control in 2004. This issue is unlikely can be rectified without substantial financial costs and time, suggesting that the Task Force members did not adequately fulfill their responsibilities, and their mistakes have already cost the DoD tens of billions of dollars.) In 2016/2017, as one of the U.S. Department of Energy’s (DoE) leading materials scientists, he was the principal investigator for the first groundbreaking research ever conducted within the DoE’s National Laboratory System in metallurgy/material science and corrosion. The project was devoted to the first-ever exploration of in-core irradiation-assisted fatigue corrosion cracking (IAFCC), the most complex and multi-variable mechanism of materials degradation. Of utmost importance, IAFCC is one of the highest priority issues that significantly affect the longevity of existing nuclear power plants. Moreover, if such a crack were to develop in any nuclear reactor on one of the 14 Ohio-class ballistic missile submarines (SSBNs), it could jeopardize the U.S. sea-based strategic deterrent. Shipilov is the author of a highly successful study he conducted for the U.S. Army that was recognized with two awards—one from the Department of Defense and the other from the Association for Materials Protection and Performance (AMPP) “for achievements in applying engineering and scientific principles to protecting and preserving the U.S. Army’s double V-hull Stryker combat vehicles.” Thanks to his efforts in 2016 and 2017, his suggested modifications enhanced soldiers’ protection against roadside bombs, improved Strykers’ availability, and boosted their overall performance (2). He also authored the first-ever report on the impact of corrosion on the readiness of U.S. naval aviation, which he prepared for the Congressional National Commission on Military Aviation Safety in February 2020 (3). (Note: All military research projects were inspired by Vice Admiral Kendall L. Card (Ret.), the former Deputy Chief of Naval Operations and Director of Naval Intelligence who requested a meeting with Shipilov in October 2015 to explore ways to improve the situation with corrosion in the U.S. military).
Shipilov received an engineer’s degree in mechanical engineering from the Moscow Institute of Petroleum and Gas Technology (now Gubkin Russian State University of Oil and Gas) and, after completing Army ROTC in Fuel Transportation, Storage, and Distribution, was commissioned as a Lieutenant Engineer Officer (Reserve) in 1981. He then pursued a two-year research internship in chemistry/materials science under Eugene D. Shchukin and earned his Ph.D. in materials and corrosion in 1987 under Viktor A. Marichev from the USSR Academy of Sciences’ Institute of Physical Chemistry, which then “was the very best organization in the world in the area of electrochemical corrosion and its fundamental as well as practical aspects” (R.W. Staehle, 2008). He holds a federal certificate of aircraft mechanic, level 3 (airframe and powerplant), and is a certified lathe operator, class 2.
Throughout his professional career, he held various positions both domestically and internationally. He has served as a professor and held visiting appointments at universities in the U.S., Canada, China, Portugal, and Russia. In the mid-1990s, he was the founding director of the Laboratory for Physical and Chemical Research in Fracture at the Russian Academy of Sciences (4) and taught at Moscow State University, the top-ranked university in Russia. Prior to that, he served as a staff scientist and an acting group leader at the Institute of Physical Chemistry of the USSR Academy of Sciences (now the Frumkin Institute of Physical Chemistry and Electrochemistry). While pursuing his Ph.D., he achieved some notable breakthroughs that were utilized at Prometey Central Research Institute of Structural Materials, the country’s leading enterprise in heavy armor and metallurgical research for shipbuilding; additionally, he worked as a part-time materials science engineer on a two-year contract with Korolev Rocket and Space Corp. Energia.
After moving to Canada in 1999, he taught for a semester at Ryerson University (now Toronto Metropolitan University), was granted a three-month fellowship by Fundação para a Ciência e a Tecnología to conduct research at Instituto Nacional de Engenharia e Tecnologia Industrial (INETI) in Lisbon and joined the faculty of the University of Calgary in 2000. From 2006–2010, he worked with Dr. Iain Le May at Metallurgical Consulting Services Ltd., which was recognized with the John Convey Innovation Award by the American Society for Metals (ASM) International in 2012. At about the same time, he was also an adjunct professor at Ryerson University. In 2011, he was honored with the title of a 3M William L. McKnight Distinguished Visiting Professor at the University of Minnesota Duluth, where he spent a year teaching in the Departments of Mechanical and Industrial Engineering and Civil Engineering. In 2012, was invited to join the Department of Materials Science and Engineering at the University of North Texas as a research professor. In 2015, he was invited to become a senior R&D staff member in corrosion science and technology at the U.S. Department of Energy’s Oak Ridge National Laboratory (ORNL), known as the “home to the nation’s most comprehensive materials research program.” In 2018, he was appointed an adjunct professor at the University of Science and Technology Beijing, which is ranked number one in the world for “Metallurgical Engineering” by the Academic Ranking of World Universities (ARWU).
In academia and the private sector, he is best known for his research on stress corrosion cracking (SCC), corrosion fatigue, hydrogen embrittlement, and predicting the corrosion performance of engineering equipment in aqueous (ambient as well as high-temperature and pressure, and H2S-containing) environments; applied fracture mechanics and designing innovative experimental equipment are also the areas he has excelled in. His research led to the development of novel crack-resistant materials for applications that require high levels of safety. Included were aluminum alloys that are utilized in the Russian modules of the International Space Station (ISS) and in the upgraded Progress M cargo spacecraft, of which 127 have been built (each costing around the equivalent of U.S.$15 million) to deliver supplies needed to sustain human life on the ISS. In addition, based on his research, high-performance HSLA steels and titanium alloys were designed for the hulls of nuclear-powered submarines, of which 17 are currently in service with the Russian Navy. It is important to note that these steels and alloys are the only structural materials specially designed to withstand environmentally assisted cracking (under specific conditions).
Among his publications are 80+ single-authored technical papers, peer-reviewed book chapters and articles in a broad array of academic journals on topics ranging from materials science, corrosion, fatigue and fracture to laboratory equipment, engineering failure analysis, and corrosion in the military. He is the principal editor of the widely used two-volume Environment-Induced Cracking of Materials (Elsevier, 2008), the most comprehensive guide on the behavior of materials under the simultaneous action of stress and chemical environments. He is also the editor of Minimizing Infrastructure Corrosion (NACE, 2009), the first data collection devoted to infrastructure reliability depending on corrosion. In 2009, he published a landmark study on the cost of corrosion in Canada, which became the key reference for the 2021 IMPACT Canada Study released by the Association for Materials Protection and Performance (AMPP) to provide “a means for [the] government and industry to coordinate the best practices for corrosion management and planning in diverse industry and municipal sectors.” He has delivered 114 invited presentations, including 14 plenary and keynote lectures, 13 distinguished lectures, and 87 invited presentations at international conferences and company seminars. Eight of his articles have been translated from Russian into English or from English into Chinese and Russian for republication abroad. Two of his articles were featured on the covers of technical journals (in 2015 and 2018), an exceptionally rare accomplishment. Moreover, one of these articles, titled “Corrosion Fatigue Crack Propagation in a Stryker Combat Vehicle,” was also displayed on the U.S. Department of Defense Corrosion Policy and Oversight homepage for 12 months from 2018 to 2019.
His reputation as the leading expert in his field has taken him to various places worldwide, including Bhabha Atomic Research Centre (BARC) in India, the Belgian Nuclear Research Centre SCK-CEN, Sevmash – the world’s largest submarine construction yard located in Russia’s Far North, and Joint Base Lewis-McChord (JBLM), the premier military installation of the U.S. Department of Defense on the West Coast. In 1992, he was invited to the Kremlin to serve as a technical consultant to Alexey V. Yablokov, a biologist by training, then President Boris Yeltsin’s State Adviser on Environmental Policy and a member of the Security Council of the Russian Federation (5). He was one of the first experts to arrive at the disaster site in Russia’s Komi Republic in 1994, where the third-largest oil spill on record occurred due to a corroded pipeline—it was before the spill made global news two months later and was investigated by Congress in 1995.
Shipilov has achieved significant success in both fundamental and applied research, as well as in developing cutting-edge technologies, often being a trailblazer in his field, both nationally and globally, right from the early stages of his career (6). In 1983, he became the first in Russia to use fracture mechanics—then still a relatively new field of mechanics concerned with the study of crack propagation in materials—to investigate corrosion fatigue, which has been (and continues to be) the primary cause of mechanical fractures in most major industries since the mid-1960s. For this project, he designed an innovative experimental setup to automatically monitor crack growth, which remained the most sensitive setup of this type in the world for over 15 years (7). In 1987, he was honored with the first Ph.D. in Russia for fracture-mechanics research on environmentally assisted cracking (8). He created the first experimental method to identify the role of hydrogen-induced cracking and stress-assisted dissolution in corrosion fatigue crack growth, which was considered “the most significant breakthrough in corrosion science since the late 1970s, requiring a ‘paradigm shift’ in the theory of corrosion, particularly in environmental cracking” (Prof. N.D. Tomashov, 1987, 1993; Prof. Ya.M. Kolotyrkin, 1992). This breakthrough earned him the 2010 Technical Achievement Award from the National Association of Corrosion Engineers (NACE) International, a professional organization serving nearly 38,000 members in over 140 countries and globally recognized as the premier authority for corrosion control solutions. In 1988, he was the first to identify SCC as the cause of inexplicable cracks in the steam generators of Soviet pressurized water nuclear reactors VVER-1000 and, in the early 1990s—at the request of Anatoly P. Aleksandrov, the President of the USSR Academy of Sciences from 1975–1986—he played a crucial role in resolving this problem (9). After 30 years, that is still the only safety-critical and widespread issue caused by SCC that has been successfully resolved in nuclear power without costly investments for materials and design replacements; also, it is worth noting that this problem, which troubled the nuclear industry for five years and cost billions of rubles (and dollars), was resolved within months. In 1993, he developed the first known full course on the physicochemical mechanics of fracture (a.k.a. fracture chemomechanics), which he taught at Moscow State University’s Faculty of Materials Science at the invitation of Dean Yuri D. Tretyakov. In 1993, he was recommended by Borys E. Paton, the President of the National Academy of Sciences of Ukraine, to coordinate research on SCC in oil and gas pipelines as part of the Russian-Ukrainian R&D Program “Highly Reliable Pipeline Transport,” signed by the prime ministers of both countries and led by Paton.


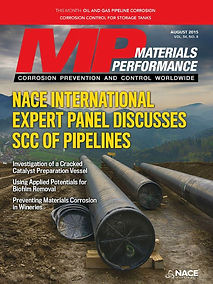
About a decade after Shipilov first concluded, in 1993, and started advocating for the recognition of the dominant role of hydrogen embrittlement and service pressure fluctuations in the ruptures of cathodically protected underground pipelines, most laboratories around the world followed his lead by reorienting their research (9). This shift has brought tremendous benefits to the global oil and gas pipeline industry. In 2004, he organized and chaired the 2nd International Conference on Environment-Induced Cracking of Metals (EICM-2), the largest gathering of EICM researchers, recognized globally as a landmark event. In 2015, along with two other world-renowned experts, he was invited to be a NACE International Expert Panelist on “Pipeline Stress Corrosion Cracking.” In 2016, he was the first expert invited to lecture on corrosion in nuclear systems at the annual DoE’s Modeling, Experimentation, and Validation (MeV) Summer School “Addressing Nuclear Fuel and Structural Materials Challenges for Current and Future Fuel Cycle Technologies.” In 2016/2017, at the request of the U.S. Senate Appropriations Subcommittee on Energy and Water Development, he led a $1-million multidisciplinary project described as “the most comprehensive study in the field of the external (soil-side) corrosion of water mains to date” by Gregg Horn of DIPRA and of which the results were intended for the U.S. Senate and House Appropriations Committees (11). In 2017, to conduct the world’s most challenging and demanding research in materials science, he designed the world’s first experimental setup that allows, for the first time, studying crack growth in reactor core materials under maximum realistic operating conditions, including intense radiation emitted by the core of an operating nuclear reactor (12).
Shipilov’s contributions to his field have earned him both national and international awards and honors. He is one of only two Canadians elected as a Fellow of both ASM International and NACE International (now known as AMPP). These titles recognize distinguished contributions to materials science and engineering and the field of corrosion and its prevention, respectively. He is also an elected Fellow of the Canadian Institute of Mining, Metallurgy and Petroleum (CIM). In October 2024, he was named the recipient of the TMS Morris Cohen Award for 2025. His many accolades include the 2023 Troconis de Rincón Field Applied Technology Award from AMPP, the Best Paper Award at the 2017 U.S. Department of Defense-Allied Nations Technical Corrosion Conference, and the 2016 CIM Fellowship Award. He also received the 2015 R.A. Brannon Award (The Signature Award of NACE International), the 2012 CIM Distinguished Lecturer Award, the 2011 G. MacDonald Young Award from ASM International, as well as the 2010 Technical Achievement Award and the 2007 Distinguished Service Award from NACE International. In 2007, he received the 2007 Morris Cohen Award from the Metallurgical Society of CIM for his “significant contributions to the achievement of corrosion science and engineering in Canada.” He has been a keynote and plenary lecturer at 13 major international meetings. ASM International selected him to present the ASM-Indian Institute of Metals Lecture in India in 2007 and the M. Brian Ives Lecture in Canada in 2005. He was also the Materials Performance and Integrity Section Luncheon Lecturer at the 43rd Annual Conference of Metallurgists (COM 2004) and the ASM Ontario Chapter Annual Keynote Lecturer in 2007. That same year, he was awarded a visiting professorship at the University of Science and Technology Beijing, funded by the Ministry of Education of the People’s Republic of China. In 2015, he received recognition from the Minister of Transport Canada, the Hon. Lisa Raitt, for his role in inspecting four railroad bridges in Toronto, which led to their extensive repairs and renovations at her request. In 2016, ORNL Director Thom Mason acknowledged his outstanding record of achievement in corrosion science and engineering, noting that it brings welcome visibility to Oak Ridge National Laboratory. Remarkably, he was the only one among over 200 Ph.D. researchers in the ORNL Materials Science and Technology Division to receive the prestigious U.S. Department of Energy's LDRD Grant in Transformational Nuclear Science and Technology that year. He was also a finalist for the MP Corrosion Innovation of the Year Award in both 2021 and 2023.
(1) Typically, such accidents and in-service failures occur on their own. They are called “unexpected,” though in most cases, they were predictable and could have been avoided. They cost Canada over $50 billion annually, plus require increased costs of equipment, maintenance, energy, and production losses. Proper or at least satisfactory investigations of such accidents and failures are very rare if they ever happen at all. No university has trained specialists in the field.
(2) Shipilov’s success in resolving a structural cracking issue on the lower-right fender of novel DVH Stryker vehicles in February 2017—which had been troubling the U.S. Army for several years, affecting the vehicles’ availability—was instrumental in securing a $258 million contract with General Dynamics Land Systems (GDLS) to upgrade 116 flat-bottom (FB) Strykers to the improved DVH configuration for the U.S. Army in June 2018. This upgrade was designated the “DVHA1 engineering change proposal (ECP) vehicle.” In 2019, the U.S. Army awarded another contract to upgrade up to 2,525 FB vehicles to the DVHA1 ECP configuration. Furthermore, a new contract worth $2.48 billion was awarded in June 2020 to produce even more upgraded DVHA1 ECP vehicles. Around the same time, in August 2019, the Canadian government awarded a C$3 billion contract to supply the Canadian Army with 360 light armored vehicles (LAVs) built on the same DVHA1 ECP platform as Stryker. In July 2022, Canada sent the first 39 of these 360 vehicles to war-torn Ukraine. In January and June 2023, the Biden administration sent 115 Strykers to Ukraine as part of its military aid. In November 2023, the Canadian government signed a new C$165 million contract for an additional 39 LAVs to replace the donated ones. In total, Ukraine received 154 Strykers.
(3) The subsequent audit in September 2021 by the DoD Office of Inspector General, which was requested by the House Armed Services Committee, recommended: “that the Commander, Naval Air Forces, assess the actions implemented to address corrosion and determine whether these actions resulted in fewer instances of corrosion, reduced costs, or improved readiness.”
(4) In this role, he was supervised by the President of the Russian Academy of Sciences, Yuri S. Osipov, and Vice President Evgeny P. Velikhov, who was the science adviser to the President of the Soviet Union, Mikhail S. Gorbachev, from 1990–1991.
(5) Shipilov’s comments on metallic corrosion in seawater played a role (not necessarily the major) in justifying Yeltsin's formation of the Government Commission on Matters Related to Radioactive Waste Disposal at Sea (“Yablokov Commission”) and preparation of a report, “Facts and Problems Related to Radioactive Waste Disposal in Seas Adjacent to the Territory of the Russian Federation” (a.k.a. “Yablokov Report”), which was discussed by Congress in 1995.
(6) At the age of 21, as part of his Engineer’s Degree thesis, he designed the first assembly line for manufacturing oil and gas drill bits with welded teeth reinforced with polycrystalline diamond (PCD) inserts. The assembly line, with newly designed equipment, semi-automatic technological processes (including welding), and machine shop layout, was recommended for practical application by a State Commission in 1981. Thanks to the success of this project, he was invited to join the USSR Academy of Sciences as a research intern, which was an exceptional achievement for an engineering graduate.
(7) This crack growth monitoring technique was patented in 1987. The world’s second setup with the same high resolution of about 0.001 mm for crack extension was developed only in the early 2000s in the U.S. The achieved level of accuracy has led to numerous breakthroughs in the field. In 2011, “for outstanding advances in the development of crack-growth characterization techniques usable in a variety of corrosive environments and their application to environment-induced cracking and related fracture phenomena,” Shipilov was elected a Fellow of NACE International, a distinction held by less than 0.5% of nearly 38,000 NACE membership. In 2017, he, with two of his summer (co-op) students—C. Brownfield and M. Wimmer of the University of Tennessee—designed a much more advanced piece of equipment to monitor crack growth in metals, which provides the world’s highest (average) crack advance resolution of about 10 nm, i.e., at least 100 times more precise than provided by the best (laboratory) experimental setups of this type in existence; notably, the achieved resolution is 2,500 times better than commercially available packages.
(8) Even today, 35+ years later, fundamental and precision research on environmentally assisted cracking (especially on corrosion fatigue) using fracture mechanics is limited to several laboratories worldwide. This is because of the high complexity of the equipment and experiments. Although dozens of doctoral degrees have been awarded in this field globally over several decades, Shipilov remains the only Ph.D. holder of Russian origin in this area of expertise.
(9) Between 1986 and 1991, a total of 34 steam generators had to be replaced due to this cracking. Their early replacement cost 5.5 billion Rubles (equivalent to U.S.$8.5 billion). If Shipilov’s advice had been taken promptly in 1988, the cost could have been less than half of what it was. However, if A.P. Aleksandrov had not requested Shipilov’s help in 1991 for work with the Russian Atomic Energy Research Center “Kurchatov Institute,” the cost would have been significantly higher... It is worth noting that in the 1940s, Aleksandrov played “a crucial and centralizing role in the former Soviet program of nuclear weapons” as a deputy to Igor V. Kurchatov, the father of the Soviet program of nuclear weapons, often compared to Robert Oppenheimer of the U.S. In 1952, Aleksandrov was appointed by Stalin to supervise the development of the USSR’s first nuclear-powered submarine with a nuclear propulsion system, K-3 Leninsky Komsomol (NATO reporting name November).
(10) Both the possibility of hydrogen embrittlement of pipeline steels and the role of service pressure fluctuations in cracking and eventually rupture of cathodically-protected oil and gas pipelines Shipilov had all evidence to insist on have been repeatedly denied, e.g., during the NACE CORROSION’96 Conference in Denver, CO, and the 1999 NACE Northern Area Eastern Conference in Ottawa, Ont. A story about the subject is ready to be made into a thriller film and deserves to be known... For example, the manuscript of Shipilov’s paper (no. IPC00-0105) titled “Critical Assessment of the Role of Cathodic Protection in Pipeline Integrity and Reliability” was first submitted for publication in the proceedings of the 3rd International Pipeline Conference (IPC 2000), held October 1–5, 2000, in Calgary, Alta. However, the paper was rejected for publication by three reviewers. Two years later, the same paper (with no changes) was submitted to the 6th International Conference on Engineering Structural Integrity Assessment, held from October 7–9, 2002, in Manchester, UK. This time, it was accepted for publication but, surprisingly, not included in the conference proceedings. Conference proceedings (without Shipilov’s paper) were published before the conference and its copy was presented to each conference attendee as part of the registration package. During the conference, Shipilov’s presentation received the most attention from attendees and was the topic of all the following discussions. As a result, the organizers had to publish a new version of the conference proceedings, which now included his paper on pp. 155–161. This was probably the only case when two versions of conference proceedings had to be published: one without one of the 25 accepted papers and another with that paper included. The updated version of Manchester’s conference proceedings can still be purchased on FESI’s website. However, Shipilov—who was not informed of the second version of conference proceedings and learned about it only in the late 2000s from Italian and Ukrainian colleagues who referred to that publication—submitted the same paper again under the title “Corrosion Protection: An + or – in Pipeline Safety and Reliability?” for the 6th International Symposium on Risk, Economy and Safety, Failure Minimization and Analysis, held March 8–12, 2004, in Cape Town, South Africa. This time, the paper was included in the conference proceedings, which were published by the same publisher (EMAS Publishing, Sheffield, UK) as the proceedings from Manchester. To
summarize, it has been many years since then, and it is now unlikely for research that contradicts Shipilov’s main ideas from 1993 to be published as credible science in an academic journal or conference proceedings.
(11) Escalating deterioration of water and sewer systems due to corrosion threatens a nation’s ability to provide safe drinking water and essential sanitation services. In addition, the cost of corrosion in the water and wastewater sector in the U.S. exceeds $70 billion per year. These two reasons explain Congress’ interest in this project.
(12) No nuclear research center/team worldwide was ready in 2016 or is prepared now (in 2024) to conduct such complex and sophisticated investigations. The lack of a similar test facility did not allow the Cooperative IASCC Research (CIR) program—an international research effort that was established “to address IASCC in light water reactor components” and sponsored by member organizations from 10 countries since 1995—to achieve its goals “to develop a mechanistic understanding of IASCC” after spending countless millions of dollars. The test facility designed by Shipilov is currently the only one worldwide that could be used to evaluate the cracking susceptibility of reactor core materials and assess the residual life of most reactors in nuclear-powered submarines and aircraft carriers in service with the U.S. and Allied navies, including Ohio-class ballistic missile submarines (SSBNs).